物流センターや生産工場においては、倉庫内の作業の中でも、特にピッキング作業時のミス防止対策に、頭を悩まされているのではないでしょうか。
出荷ミスは取引先とのトラブルの原因となってしまいますので、小さなミスでも見過ごすことはできません。
ピッキング作業時にミスが起こってしまう要因はどこにあるのか、またミスを防ぐためにはどうしたらよいのか、その対処法について解説します。
作業時に発生するピッキングミスの要因
ピッキング時に発生してしまうミスは、個人の問題から倉庫全体の問題など、様々な要因が考えられます。
その中でも、主となる要因について見ていきましょう。
作業ルールが徹底していない
ピッキングは、ピッキングリストに基づいて商品をピックアップするというシンプルな作業です。
簡単な作業であるが故に、担当者それぞれがマイルールに基づいて作業を行うため、ミスが発生すると、その原因がどこにあるのかを特定することが困難になります。
作業ルールを明確にし、そのルールを適切に守りながら作業を進めることが、ミスを防ぐ重要な要因になります。
また、作業ルールを明確にすることでマニュアルの作成も可能となり、マニュアルがあることで作業ルールを見直す機会を持つことにもつながります。
人によってやり方が異なる
作業者ごとにピッキングの方法が違うことは、ミスの増加を招きます。
新人教育を担当する人や配属された作業エリアにおける上司などの作業手順に、異なる点があるのであれば、新人作業者は混乱してしまいます。
ピッキングは繰り返しの作業ですので、作業者全員が同じ認識を持つことが重要です。
ロケーションと作業が最適化されていない
取り扱っている商品名が似ていたり、類似商品があったりする場合は、見間違いによるミスが発生しやすくなります。
しっかり型番や品番まで確認して作業を進めれば改善することが可能ですが、熟練者であればあるほど、一目見ただけで直観的な判断をしてしまい、その結果ミスを起こしてしまう可能性があります。
① 似たような名称の商品は距離を置いて配置する
② 見間違いをなくすような商品配置を行いましょう
また、ピッキングエリアをしっかり確保せず、あちこちに商品が配置してあると、作業者の移動距離も長くなり、効率も悪くなりますしミスも誘発してしまいます。
作業を行う場所はある程度のスペースを確保するなど、少しでも作業者が仕事をしやすいような環境を整えることができれば、ミスを減らすことができるでしょう。
ポカミスをしやすい環境
ミスをしてはいけないと思うと、人によっては萎縮してしまう可能性があります。
思いつめると判断力が低下していまい、しなくても良いミスをする可能性も高くなるでしょう。
もちろんミスはすべきではありませんが、ミスを素直に報告しやすい環境を整えておくことも最終的にはポカミス防止に繋がっていきます。
お客様の現場に合わせた改善提案もご対応いたします。
ご希望の際は「お問い合わせ」から「改善提案希望」と記入してください。
担当者からご連絡いたします。
ピッキングミスによるトラブルとは?
最初に、ピッキングミスによって起こるトラブルについて、しっかりと確認しておきましょう。ことの重大さがわからなければ、意識的に改善することもありません。
ピッキングミスはちょっとしたミスではなく、非常に大きなミスだということを理解してください。
信用を失う
ピッキングミスで、最も大きな被害は取引先からの信用を失うということでしょう。
納品された商品の数が少ないことが原因で、十分な仕事ができないなど取引先に不利益を与えてしまいます。
一度、失った信用を取り戻すことは、簡単なことではありません。
下手をすれば、一生、元に戻らない可能性もあることを忘れないようにしましょう。
作業負担が増える
ミスをしたからには、そのミスの埋め合わせをするための作業を行わなければなりません。
予定外の仕事をしなければならなくなるだけでなく、迅速な対応を求められるので作業負担が大きく増えてしまうでしょう。
作業のコストが増える
ピッキングミスの対応はもちろんしなければなりませんが、だからと言って、通常の業務の進行を遅らせることはできません。
したがって、ミスの処理をするための人員を割かなければなりません。
人手が必要になるほど、作業コストも増えていきますので、会社としての利益も損なわれていきます。
ピッキングミスをなくすための改善策
ピッキング作業におけるミスの原因がわかったら、次は作業中のミスを減らすための方法を考えなければなりません。
それぞれの倉庫で抱えている問題によって、実施すべき改善策は違います。
自社の抱える問題をしっかりと把握した上で、改善策を検討していきましょう。
ピッキングシステムの導入を検討してみる
ピッキングシステムを導入することで、作業を簡略化することができます。
作業者にかかる負担を大きく減らすことができるので、自然とミスを減らすことができるでしょう。
なお、ピッキングシステムはミスを減らすだけでなく、作業の効率化にもつながります。様々なメリットがありますので、導入を強くおすすめします。
ピッキング作業に適した環境に整備する
一流の職人が道具にこだわりを持つように、仕事をする環境を整えることは重要です。
もちろん、作業者のレベル自体を底上げすることは重要ですが、すぐにスキルアップできるわけではありません。
それより、働きやすい環境を作った方が、はるかに早く問題を解決することができるでしょう。
棚や商品の配置を換える
現在の配置がベストかどうかを見つめ直すことで、作業者の働きやすさは大きく変わります。
よく利用する商品とそうでないもので配置変えを行うことや、商品を探しやすいように工夫された配置を考えましょう。
類似品を離す
似ている商品が隣り合って並べてあると、疲れているときなどに、ついうっかり間違った商品を手に取ってしまう可能性が高くなります。
ピッキングミスが多い商品に関するデータを集めて、間違いが多いもの同士が近くに配置されないようにしましょう。
情報を共有する
三人寄れば文殊の知恵と昔から言うように、作業者の情報を共有しあうことで、新たに解決策を見つけられる可能性が高まります。
独自で考えたミスを防ぐ方法など、どんな小さな情報でも共有するようにしましょう。
入庫作業の正確性を再度確かめる
ピッキングのミスは、ピッキング時に起こるとは限りません。
商品を保管場所に入庫するときに、すでに間違った商品が保管されていたというケースも、ピッキングミスとになります。
ミスの原因がどこにあるのかを調べることは重要な作業です。
手間のかかる作業ですが、しっかりと確認しておくべきでしょう。
お客様の現場に合わせた改善提案もご対応いたします。
ご希望の際は「お問い合わせ」から「改善提案希望」と記入してください。
担当者からご連絡いたします。
タカハタ電子のデジタルピッキングシステムでミスを減らす
○ハンディーターミナルシステムを連携したポカよけシステムの設計
・ピッキングした製品に間違いが無いかをスキャンする事で正確さを向上させる。
・棚入庫時にハンディーターミナルで間口のロケーションバーコードを読むことで、入庫ロケーションに間違いが無いかを確認する。
・社内バーコードを貼り付け、製品の所在を明確にし、先入れ先出しの正確性を確保する。さらに、ロット管理が確保されるので、有効期限や消費期限の管理も可能になる。
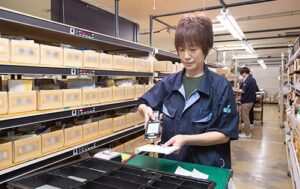
出庫作業例
○タブレットマルチオーダーピッキングシステムを活用したシステム
・複数オーダー同時に仕分けを行うため、類似オーダーをソートする機能を設けることでなるべく多くの間口にヒットさせる事が出来る様になり、取り忘れは減少する。さらに同じピッキング製品を同時に仕分け可能なため、ピッキング効率もあがる。
・間口の入れ間違い防止のため、複数オーダーピッキング終了後にハンディーターミナルを用いて検品作業を行う。
○5色5ボタン式の使用時の工夫。
・作業中に発生しがちな担当色の失念を防止するため、集品カートと担当色を同じ色で着色する。
・担当色を同じ色の腕章を付けて作業。
・作業日は全て同じ色で作業を実施する。